Introduction
Facility managers are under pressure to squeeze every extra year out of their platforms, catwalks, and trench covers while raw‑material prices and maintenance labor keep climbing. That reality has turned the humble floor grating into a board‑room discussion about return on investment (ROI). Fiberglass alternatives promise decades without rust, paint, or shutdowns—but how do you translate those claims into real cash savings and choose reliable fiberglass floor grating suppliers who deliver?
Unicomposite, an ISO‑certified pultrusion manufacturer headquartered in China, illustrates how a supplier’s engineering depth and vertically integrated factory can tilt the ROI equation in your favor by shortening lead times, tailoring resin systems, and backing performance with third‑party data.
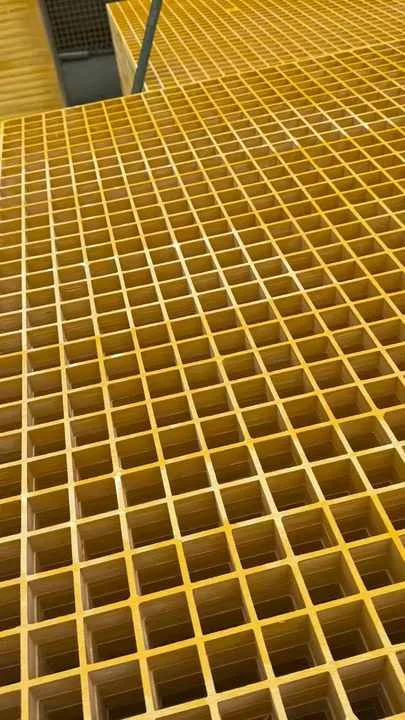
fiberglass floor grating suppliers
Why ROI Matters When Sourcing Fiberglass Floor Grating
Direct Cost Components
Price per square foot matters, but it is only the first of four checks you should run: resin/glass content, freight class, import tariffs, and tooling for custom panel sizes. A molded 38 × 38 mm FRP panel can cost 15 % more up‑front than galvanized steel of similar load rating, yet the fiberglass panel ships at roughly one‑quarter the weight, cutting freight and crane rental fees Unicomposite.
Indirect Cost Drivers
Lifecycle expenses dwarf purchase price. FRP never rusts, so it avoids media blasting, repainting, and hot‑work permits. In plants where downtime exceeds $10 k per hour, a single weekend shutdown to replace corroded steel grating wipes out any initial savings. Slip resistance and dielectric safety also reduce recordable incidents—another hidden ROI lever.
Data Point: 5‑Year TCO Comparison
According to a 2024 multi‑site study compiled by a global composites trade association, FRP grating delivered a 37 % lower total cost of ownership than steel when factoring maintenance coatings, labor, and replacement panels.
Reliability Signals to Look for in Suppliers
Certifications & Standards
Start with ISO 9001 for quality management and ISO 14001 for environmental practices. For product conformity, ASTM F3059 outlines performance tests for pedestrian FRP grating, while EN 13706 grades pultruded profiles. Ask the supplier for recent third‑party test reports, not just marketing brochures.
Production Capabilities & QA
Reliable fiberglass floor grating suppliers run continuous pultrusion lines with online glass‑fiber wet‑out monitoring and post‑cure ovens that lock in bar‑to‑bar consistency. Unicomposite operates automated tensile and fire‑resistance labs in‑house, trimming two weeks off typical external testing cycles and giving buyers early sight of load‑span tables.
Engineering Support & Custom Profiles
An underrated reliability metric is the willingness to co‑engineer bespoke profiles. When an aquaculture OEM needed a non‑skid, food‑safe panel, Unicomposite swapped the standard isophthalic resin for an FDA‑approved vinyl‑ester blend and milled radiused edge caps—without new tooling charges.
Case Study: Cutting Lifetime Costs by 27 % with a Power‑Utility Retrofit
Project Snapshot
A western US power utility retrofitted the inspection platforms of a 50 MW cooling‑tower cell with pultruded fiberglass grating. The previous steel panels had required two repaint cycles in eight years and showed through‑hole corrosion at the clip seats.
Problem → Solution Path
Faced with another $120 k repaint and OSHA slip‑resistance citation, the maintenance engineer issued an RFQ for FRP alternatives. Out of six bidders, two delivered performance data and on‑site mock‑ups; the contract went to a supplier offering UV‑stable, fire‑retardant grating certified to ASTM E84 Class 1.
Quantified Outcomes
Installation finished two days ahead of schedule because the lighter panels allowed man‑lift placement instead of crane lifts. The weight reduction unlocked a 5 % fan‑speed increase, boosting airflow efficiency. Combining energy gains and avoided maintenance, finance calculated a full payback in 18 months and net lifetime savings of 27 % over coated steel.
“We haven’t budgeted a single dollar for platform maintenance since the switch, and that’s unheard‑of in a coastal plant,” — Maintenance supervisor, anonymized utility (2025 exit interview).
Step‑by‑Step Supplier Evaluation Workflow
RFI/RFQ Checklist
Resin system & glass content (list percentages).
Load tables for your span and deflection criteria.
Lead times for molded vs. pultruded SKUs.
Compliance docs (ISO certs, ASTM tests, SDS sheets).
Plant Audit or Virtual Tour Tips
If travel budgets are tight, request a 30‑minute live video walk‑through of pultrusion lines, raw‑material storage, and QA labs. Look for barcode traceability on creels and color‑coded resin drums—small tells of a disciplined operation.
Sample & Third‑Party Testing Protocols
Always pull an extra 2 % witness coupons from production panels and ship them to an accredited lab for flexural strength and fire testing. Genuine suppliers embrace this because it validates their own data.
Negotiating Terms for Maximum ROI
Volume Pricing vs. Blanket Orders
Annual volume forecasts enable suppliers to pre‑buy glass roving, often shaving 8–10 % off unit cost. If project volume is uncertain, negotiate a six‑month blanket order with release windows tied to your construction milestones.
Warranty & Service‑Level Clauses
Push for written warranties covering UV degradation, colorfastness, and surface‑grit retention for at least 15 years. Also pin down maximum response times for replacement panels in the event of freight damage.
Logistics & Incoterms That Protect Cash Flow
When sourcing overseas, consider DDP terms for smaller orders to avoid surprise duty bills. For container‑load shipments, switching to FOB often yields better control of ocean freight rates, especially when steel and resin markets fluctuate.
Conclusion
ROI shoots upward when you align high‑performance material with a supplier who proves reliability through certifications, transparent QA, and collaborative engineering. Use the evaluation workflow above to benchmark contenders, and keep forward‑thinking suppliers like Unicomposite on your shortlist. Ready to quantify savings on your next platform or walkway project? Request a technical review or RFQ today.
Frequently Asked Questions
Q1. How long does fiberglass grating realistically last in a chemical plant?
Properly specified vinyl‑ester FRP panels have documented service lives exceeding 25 years in pH‑extreme environments, thanks to full‑depth corrosion resistance and UV inhibitors.
Q2. Can I get custom colors or surface grit levels?
Yes. Pultrusion and molding processes allow integral pigments and multiple grit sizes, so you can match corporate safety colors or adjust slip resistance without post‑coating.
Q3. What is the typical lead time for a full container load?
Standard mesh panels usually ship in 3–4 weeks ex‑works. Add two weeks for ocean transit to West Coast US ports and one week for customs clearance.
Q4. Do fiberglass floor grating suppliers provide engineering calculations?
Reputable suppliers issue load‑span tables and can run finite‑element checks on unusual spans, often within 48 hours of receiving your specs.
Q5. How do I verify fire performance claims?
Ask for ASTM E84 and EN 13501 test reports from an accredited lab and, if needed, send witness samples for independent confirmation.