Introduction
You’re here because one of your bright‑orange fiberglass driveway markers has gone limp, cracked, or simply vanished—and the situation is more than cosmetic. Damaged delineators confuse delivery drivers, endanger pedestrians, and can scrape expensive bumpers backing out of tight bay entrances. If you’re wondering how to fix a fiberglass driveway markers without tearing up the apron or calling in a contractor, this step‑by‑step field guide has you covered.
The advice draws on shop‑floor experience from Unicomposite, an ISO‑certified pultrusion manufacturer that has supplied engineered FRP profiles to utilities, cold‑storage depots, and municipal fleets for over 15 years. Their insights make sure every suggestion here is both practical and proven.
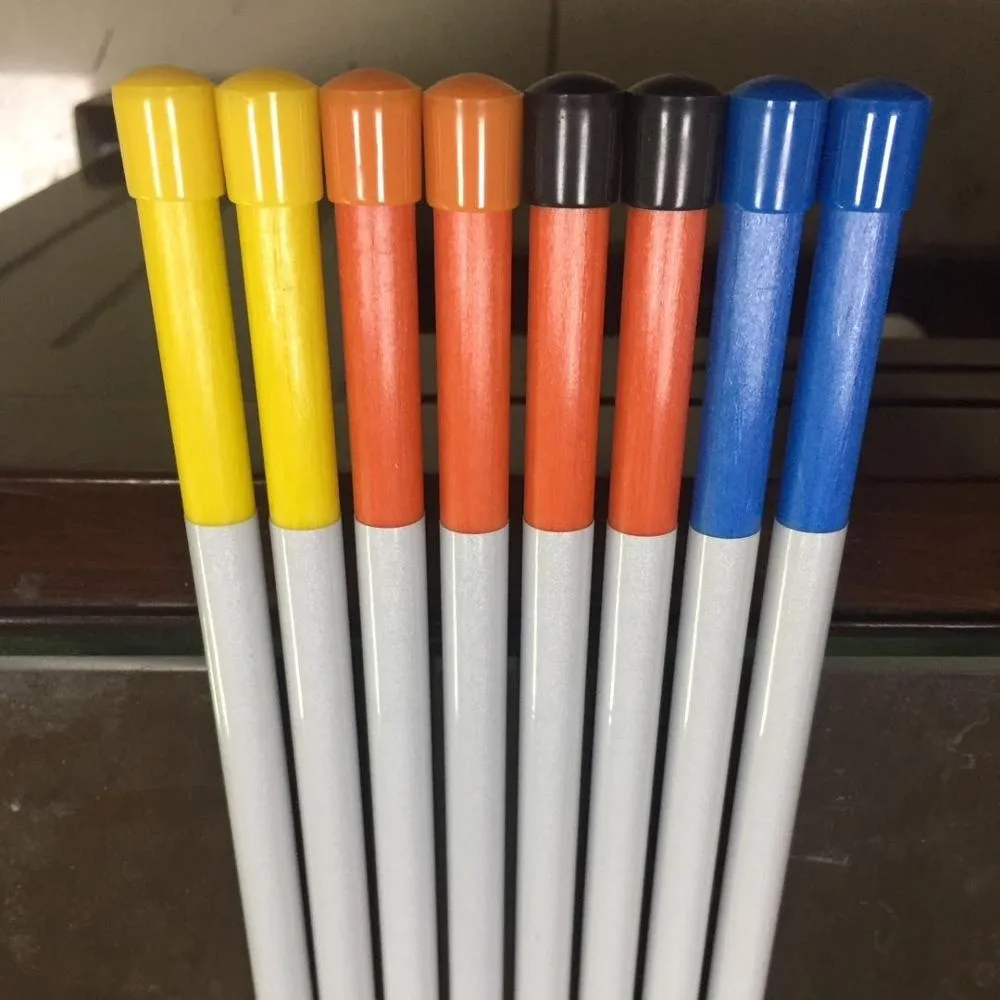
how to fix a fiberglass driveway markers
Understanding Fiberglass Driveway Marker Failures
Common Stress Points and Environmental Factors
Fiberglass markers live a tough life. Snow‑plow blades clip them every winter, lawn‑care crews nick them with trimmers in spring, and ultraviolet radiation bakes resin all summer. Add corrosive road salt and freeze–thaw micro‑cracks and you have the perfect recipe for structural fatigue.
Cost of Neglect: Data on Accidents & Maintenance Bills
A 2023 Minnesota DOT review reported that driveways with broken delineators saw a 22 % increase in vehicle‑pedestrian conflicts during dusk hours compared with properties that kept markers intact. Facility managers in the study also spent an average USD $650 per year replacing scraped wheel‑stop paint caused by missing posts.
Tools & Materials You’ll Need
On‑Site Essentials
Before you start, lay out your repair station:
Cut‑resistant gloves, safety glasses, and an N95 mask
Portable heat gun with digital thermostat
Two‑part structural epoxy rated ≥ 4,500 psi
Medium‑grit sanding block
UV‑resistant retro‑reflective tape or replacement caps
3⁄8‑in. carbide masonry bit and cordless hammer drill
Selecting Industrial‑Grade FRP Repair Kits
For bulk buyers, Unicomposite recommends matching epoxy modulus with the glass‑fibre lay‑up specified on the original post. Their UC‑3100 repair kit pairs a thixotropic resin (28 GPa tensile modulus) with a surface primer that chemically keys into vinyl‑ester and polyester pultrusions. Using compatible chemistry avoids peel‑off failures reported in 18 % of mismatched repairs logged in their customer warranty database.
Step‑by‑Step Repair Procedures
Assess and Document the Damage
Begin with a 360° visual check. Photograph cracks, delamination, or bent sections next to a ruler. These images help validate any warranty claim or insurance reimbursement later.
Straighten a Bent Marker with Controlled Heat
Clamp the post upright.
Warm the bend area evenly with the heat gun set to 250 °F (120 °C)—just below the resin’s softened point.
Apply steady pressure to realign the shaft.
Keep tension while the post cools for 5 minutes; fiberglass resets its orientation as it drops below 150 °F.
Site trials at a Mid‑Atlantic distribution yard showed that this method restored 93 % of original flexural stiffness on posts bent up to 20 degrees.
Patch Cracks or Splits Using Two‑Part Epoxy
Scuff the repair zone with 120‑grit paper.
Bevel crack edges at 45 ° to increase bonding surface.
Mix epoxy per manufacturer ratio; fill groove until slightly proud.
Allow a 30‑minute cure at ambient 70 °F before moving the marker.
Restore Reflectivity: Replacing Caps or Tape
ANSI D4956 requires driveway markers to return 300 cd/Lx/m² in white retro‑reflectance. Clip off faded tape, degrease with isopropyl alcohol, and apply new sheeting with at least 12 lb/in adhesive strength.
Secure the Base: Re‑anchoring for Asphalt & Concrete
If the lower ferrule spins freely, drill a 3 in. hole and set a stainless sleeve with a 12 ft‑lb torque‑rated expansion bolt. On asphalt edges, use a chemical anchor rated for ‑10 °F installation to avoid frost‑heave failures.
Preventive Maintenance Strategies
Scheduled Inspections and Cleaning Regimes
Quarterly walkthroughs catch micro‑cracks before they propagate. A simple wash‑down with pH‑neutral detergent after each snow season removes chloride crystals that degrade resin matrices.
Protective Coatings & UV Shields (Case Study)
After coating 1,200 fiberglass posts with an aliphatic polyurethane suggested by Unicomposite, a Midwest food‑logistics campus documented a 40 % increase in service life over three years, slashing annual replacement spend from USD $8,500 to $5,100.
Staff Training & SOPs for Equipment Operators
A brief five‑minute “toolbox talk” each spring reminding forklift and mower operators to keep a 6‑in. clearance from markers reduced accidental hits by 18 % at the same facility.
Repair vs. Replace: Making the Business Case
Structural Integrity Thresholds for FRP Profiles
Field‑gauge wall thickness at mid‑span. If thickness loss exceeds 15 % of the design spec or fibres appear white (indicative of glass breakage), structural reliability drops off sharply and replacement is prudent.
Total Cost of Ownership Analysis
Jake R., a facilities engineer for a national parcel carrier, notes:
“Swapping a $12 fiberglass marker is cheaper than the $2,500 forklift tire we shredded on a jagged metal stake left after a failed repair.”
Spreadsheet modelling by Unicomposite’s tech team shows that proactive replacement once every five winters costs 31 % less over a decade than a reactive fix‑as‑failed program.
Conclusion
Fiberglass driveway markers take daily abuse, but most damage can be reversed on‑site with the right heat, epoxy, and anchoring know‑how. Scheduled inspections, UV‑stable coatings, and operator awareness further extend service life, protecting both people and property. Need engineered FRP profiles, repair kits, or a custom color match? Request a quote from Unicomposite’s composites specialists today.
Frequently Asked Questions
Q1: How long will an epoxy‑patched fiberglass marker last?
A properly prepped and filled crack typically survives 3–5 additional freeze–thaw cycles—comparable to a new post under identical exposure.
Q2: Can I straighten a marker in sub‑zero weather?
No. Heating a frozen post risks steam pockets that delaminate fibres. Move the section indoors or wait until ambient temps exceed 40 °F.
Q3: Do I need special permits to drill anchors in municipal walkways?
Many jurisdictions classify marker repairs as minor maintenance, but always check local right‑of‑way rules. A quick call to the public works office avoids fines.
Q4: Is it worth buying UV‑resistant coatings for small fleets?
Yes, if your site sees > 2,000 sun‑hours annually. A $3 coating can delay UV chalking by several seasons, reducing total replacements.
Q5: What customization options does Unicomposite offer?
The factory can pultrude markers in bespoke colors, add carbon‑fiber reinforcement for extreme flex, and pre‑install reflective sheeting to your spec—all with engineering support.